普通快滤池增加气水反冲洗功能探讨
发布时间:
2024-03-09
浏览
次
如果您想了解我们的产品,欢迎随时拨打我公司的销售热线,或点击下方按钮免费咨询!
电话咨询即刻享受本月价格折扣!
普通快滤池改造气水反冲洗,难度在滤池结构上。下文简要介绍大阻力配水系统和旅途式小阻力配水系统的特点,以及将二者相结合的改造方式。
一、大阻力配水系统
普通快滤池采用的大阻力配水系统,一般滤池底板设配水干管(渠)和配水支管,支管上45度位置开孔,干管(渠)和支管呈“丰”字形,又称“丰”形大阻力配水。反冲洗时,水通过“丰”形管及上开孔冲洗滤料,实现水冲洗功能。为防止滤池滤料流入配水管中,配水系统和滤料间设有承托层。一般考虑承托层厚500mm,滤料层厚度不小于700mm,总厚度(从滤池底板至滤料层顶)1200mm。用于排除洗池水的洗砂排水槽,槽底距滤料层425mm(以700mm滤料层厚、50%膨胀率计)。
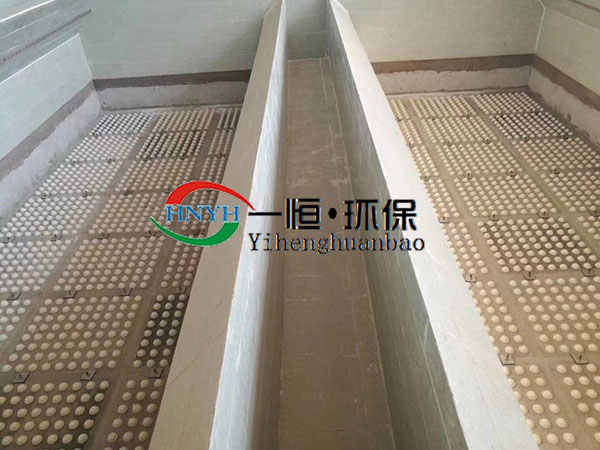
二、滤头式小阻力配水系统
滤头式小阻力配水系统,是在距离滤池底板600mm(根据设计调整)处,设多孔板,多孔板上安装滤头,板与板间缝隙密封。多孔板与滤池底板之间形成的空间称作配水室,配水室的顶部和底部分别开有配气孔和配水孔。反冲洗时,可分别进行气冲洗、气水冲洗和水漂洗,通过滤头上的缝隙吹洗滤料。由于滤头缝隙0.5mm左右,可大大缩小滤头与滤料之间承托层厚度——通常采用100mm厚卵石层,滤料层厚度不小于800mm(事实上笔者见过的气水反冲洗滤池滤料层厚度,小的在1200mm,大的可达2000mm),总厚度(从滤池底板至滤料层顶)不小于1500mm。
三、普通快滤池实现气水反冲洗
从上述两种配水方式可以看出,普通考虑增加气水反冲洗功能,如果参照多孔板滤头式小阻力系统,从池体内部空间上,一方面既有总厚度1200mm与低限的1500mm存在300mm的差异,另一方面普通快滤池排水槽与滤料层间空间有限(槽底距滤料层425mm),若提高滤料层高度,排水槽势必影响反冲洗效果;从池体结构上,小阻力配水的配气孔设在配水室顶部,需在快滤池中央干渠上开孔,进行结构变动,中央干渠通常情况下是池体承重混凝土墙,过多开孔会影响土建结构安全性。这就从池体内部空间及墙体安全两方面局限了改造。气水反冲洗的配水方式另有一种“丰”字管道式,如图,连接中央渠的“丰”字形大阻力配水管与连接中央管道的“丰”字形配气管交叠错落布置,水、气各由一套独立的系统,可分别实现气水反冲洗。这种方式较好地解决了空间、结构方面难题,可在滤池结构近乎不变的情况下实现气水反冲洗,其缺点一是由于水管道依旧采用大阻力配水系统,所以仍旧需要卵石承托层,对气压力要求较高;二是独立的气管路没有排气过程,管道中的气体随着滤池运行易跑到滤料中。
笔者有幸参观了国外某水厂,该水厂始建于十九世纪五十年代,其滤池为普通水洗砂滤池,存在冲洗不干净、滤料结泥、运行周期短等问题,后改造为气水反冲洗滤池。至笔者参观时已改造运行多年,增加了气洗功能,提高了反冲洗效果,有效减小滤料含泥量。该技术保留了大阻力配水系统,植入了滤头,不仅滤池原结构满足要求,且跟水共用一套管路,不存在残存其他问题;因着滤头的使用,取消了卵石承托层,还可适当增加滤料层厚度,极度贴近了V型滤池效果。
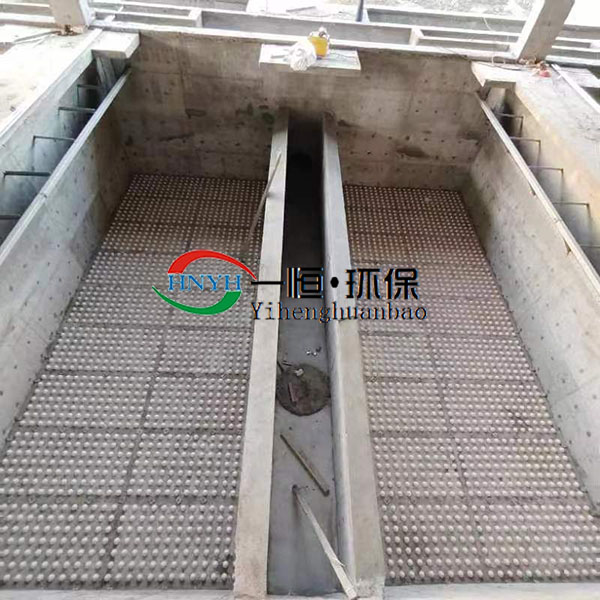
该水厂共用18组砂滤池,每两组滤池共用一个进出水渠,滤池两侧分布,单侧面积4.2*8.45。改造后的滤池底板纵向水平铺设直接100mm的PVC滤水管作为滤水管及主布气管,每根管道中部三通管,向下接入滤池底板上的清水渠内。每根滤水管顶部均匀开孔,插入滤头并焊接牢固。滤头数量为每平方米40个。同时滤水管上部左右两侧中间部位接出一根直接20mm管道作为支气管,每根支气管纵向接入上部的分气管中分气管与“丰”字行滤水管呈垂直分布与清水渠平行。两根分气管再汇合成一条气路总管,穿过池壁与管廊中的供气干管连接。滤头以下至滤池底板间现浇混凝土以稳固滤水管及滤头。混凝土上滤头间铺设100mm厚卵石层(2mm),之上再铺设800mm厚砂滤料。
滤池处于过滤期时,沉淀后的水通过进水渠进入滤池,从上至下流经滤料后,通过滤头进入滤水管并汇集到清水渠内。该水厂沉淀后水的浊度控制在0.2~2NTU之间,滤池绿色为6.32m/h,滤后水浊度控制在0.1~1NTU,滤池运行周期为48小时。滤池处于反冲洗期时,关闭进水闸,打开排水闸,进入反冲洗阶段。首先进行气冲洗:压缩空气经气路总管、总进气管、分进气管、支进气管进入滤水管,再通过滤头排出,对滤料进行气洗。气洗强度为52m3/h/m2,历史5分钟。气冲洗结束后进入水冲洗阶段:反冲洗水通过中央水渠、三通管流入滤水管,通过滤头流出对滤料进行冲洗。水洗强度为49.3 m3/h/m2,历史6分钟。完成一组反冲洗后启动另外一组滤池反冲洗,冲洗后废水经排水渠排空。两组滤池反洗结束后,关闭排水闸、打开进水闸,滤池恢复过滤。参观的两组滤池,其反冲洗的气洗布气均匀、水洗漂洗干净。四、小试测试
笔者利用国内某水厂已有滤柱模型改进后进行了模拟实验。原滤柱模型为圆形有机玻璃材质,内径DN280,内部构成包括滤水管直径及间隔、洗砂排水槽、空间高度等,按照生产滤池实际尺寸制作。实验用滤头由自生产厂家提供,滤帽直径70mm,滤柄直径25mm,壁厚2mm,滤缝宽0.25mm。以每平方米40个计应设滤头2.5个,实际内应设3个滤头,每平方米50个滤头。限于滤柱圆形外观、内设两根滤水管,所以3个滤头呈星型分布,各滤头间距较近,在反冲洗过程中相互干扰。气洗用压缩空气来源于库存空压泵,在出气管上设压力转换阀,反冲洗水来自高压水管路。在整个反冲洗过程中空气压力稳定性差,气量无法控制,以水面在滤水管中低于滤柄进气口高于滤柄口作为控制原则;水洗通过水表控制水量。因冲洗控制方式的原因,在气冲洗时出现砂滤料膨胀。滤柱设在滤站管廊中,过滤水来源同滤池,滤后设浊度仪,反冲洗周期以滤后水浊度等同于滤池浊度为依据。通过为期两个月的实验,与生产滤池运行情况相比,结论如下:
1、在相同的过滤水及滤后水浊度的情况下,其过滤周期延长1/3,反冲洗时间节约5分钟(滤池水洗12分钟);
2、虽然滤后水浊度近似于滤池,考虑到滤柱为有机玻璃材质,内壁光滑,在整个运行周期内都有过滤水短流顺内壁直接流至滤头对浊度的不利影响,若运用到生产实际滤后水浊度将有所降低;
3、由于滤头设置数量(3个)高于计算值(2.5个),实际过滤水量大于同步生产滤池;
4、由于承托层厚度的减少,使得滤料层高度增加成為可能,控制滤池顶与原滤料层相同,增加了400mm,滤床厚度达到1100mm;
5、由于滤床厚度的增加使得均质滤料成为可能。实验期间更换了部分滤料,滤料粒径加大,由于水厂没有均质滤料,只能从既有级配滤料中筛捡,筛出量低。从实际运行效果看,对滤后水浊度没有影响,但滤柱运行周期延长了。
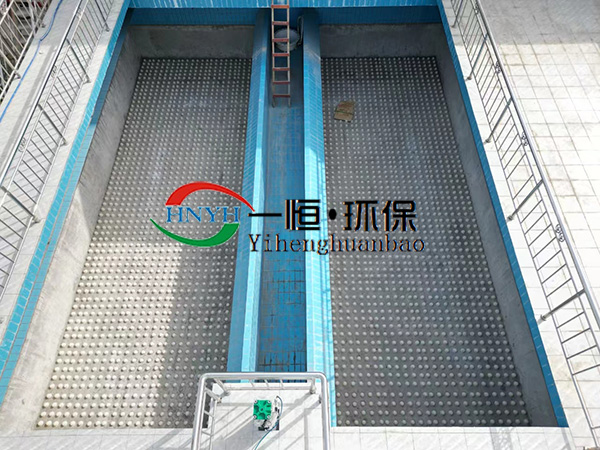
五、总结
笔者认为该改造方式存在以下优势:
1、由于主管道仍旧为“丰”形大阻力配水方式,气管道采用滤水管顶部钻孔、布气,空气从滤料层接入,避免了对清水渠的改动;
2、气洗系统主要布置在滤池内部,仅有一条总进气管需穿过池壁,对原有滤池池壁结构的改动降到了低;
3、采用现浇混凝土方式,使滤池的滤水管、滤头、分气管焊接处连成一个整体,增加了连接稳固性,避免长期使用开焊;
4、采用滤头装置,上部配置滤料层时紧铺装100mm厚卵石层,远小于原来大阻力配水系统的卵石层厚度(500mm),可适当增加滤料层厚度;
5、采用滤头装置,增加了滤水及反冲洗的均匀性;
6、由于滤头的采用,砂滤料可考虑均质滤料,而非原来的级配滤料,可延长过滤周期;
7、由于增加了气冲洗,提高反冲洗滤料洁净度,同时减少了反冲洗用水。
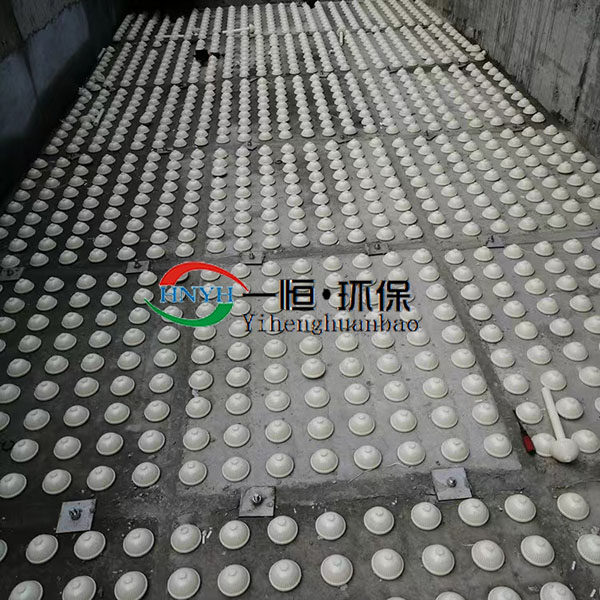
但是,该改造方式也存在一定的缺点,主要在施工阶段及日后维修维护方面:
1、与传统的气水反冲洗滤池相比,改造后的滤池反冲洗,独立实现气洗、水洗,没有气水混洗阶段;
2、由于进气管滤水管之间的连通是通过20mm的支气管,在焊接施工时,需要较高的施工精度;
3、与传统的预制支撑板不同,该工艺需要现浇滤头至底板,对滤头的保护及高程控制较高;
4、在实际调试中,不同于实验时的透明材质可实际观察进气孔、滤柄口以控制气量,需摸索出气洗时滤水管内水面佳控制点;
5、由于采用整体浇筑方式,一旦某滤头或滤水管出现问题时,无法单独更换及维修。
尽管该技术存在上诉缺点,但笔者认为这仍是一个老滤池适应当前水质要求的投资少、见效快的改造方式。该技术的大优势在于摒弃了常规滤头设计中的配水室,将滤头根植于大阻力配水系统的配水管中,使大阻力、小阻力配水系统特点相结合,从而使滤池实现气水反冲洗、均质滤料、延长过滤周期、提高滤料洁净度。